铝压铸件缺陷-氧化夹渣的预防措施
摘要:铝合金压铸件浇口夹渣多为类似缩孔、油污和冷硬层3种形式。引起夹渣的原因主要是压铸模具温度过高、冲头油过量和Al液含渣量高等。解决缩孔类夹渣,主要从降低压铸模具温度入手;油污类...
铝合金压铸缺陷-氧化夹渣的预防措施:
严格控制铝合金铸件熔炼工艺,快速熔炼,减少氧化,除渣彻底。Al-Mg合金必须在覆盖剂下熔炼。 熔炉、工具要清洁,不得有氧化物,并应预热,涂料涂后应烘干使用。 设计的浇注系统必须有稳流、缓冲、撇渣能力。 采用倾斜浇注系统,液流稳定,不产生二次氧化。 选用的涂料粘附力要强,浇注过程中不产生剥落而进入铝合金铸件中形成夹渣。
铝合金压铸件一般用ADC11或者ADC12,ADC11的化学成分如下:
ADC11的化学成分
夹渣形态及形成机理
通过对铝合金压铸的报废件分析,浇口夹渣主要有3种形态:缩孔类、油污类和冷硬层。其中以油污类的夹渣数量居多,占夹渣总数的60%以上;冷硬层占夹渣总数的35%左右;而缩孔类占夹渣总数的5%。
通过对铝合金压铸的报废件分析,浇口夹渣主要有3种形态:缩孔类、油污类和冷硬层。其中以油污类的夹渣数量居多,占夹渣总数的60%以上;冷硬层占夹渣总数的35%左右;而缩孔类占夹渣总数的5%。
铝合金压铸缺陷-氧化夹渣原因:
- 炉料不清洁,回炉料使用量过多
- 浇注系统设计不良
- 合金液中的熔渣未清除干净
- 浇注操作不当,带入夹渣
- 精炼变质处理后静置时间不够
通过对铝合金压铸的报废件分析,浇口夹渣主要有3种形态:缩孔类、油污类和冷硬层。其中以油污类的夹渣数量居多,占夹渣总数的60%以上;冷硬层占夹渣总数的35%左右;而缩孔类占夹渣总数的5%。
1、类似缩孔缺陷
当敲掉铝合金压铸件浇道料饼后,浇口处出现呈不规则形状、内部比较干净、表面粗糙的类似缩孔状的孔洞。缩孔类夹渣的铝合金压铸件浇口表面凹陷,打磨涂装后外观仍不光洁。产生原因是内浇口温度比较高(实测最高模温为380℃),是最后凝固的部位,造成该处Al液来不及补缩,产生缩孔缺陷。
2、油污类缺陷
每一铸造循环需向冲头加注润滑油,冲头油在Al液浇注后没有完全燃烧,被包裹在Al液中形成杂质一起填充到型腔。由于包裹有冲头油的Al液温度较低,会较早凝固,流动速度慢,因而在填充末了时停留在产品末端。加之内浇口截面积小,流动阻力大,这部分包裹有冲头油且提前凝固了的Al液杂质更不容易通过,停滞于内浇口附近。敲掉料饼后,在内浇口处呈现黑色孔洞,其内壁粗糙,表面有明显油污。检查浇口和料饼夹渣情况,同样发现此类杂质。当敲掉铝合金压铸件浇道料饼后,浇口处出现呈不规则形状、内部比较干净、表面粗糙的类似缩孔状的孔洞。缩孔类夹渣的铝合金压铸件浇口表面凹陷,打磨涂装后外观仍不光洁。产生原因是内浇口温度比较高(实测最高模温为380℃),是最后凝固的部位,造成该处Al液来不及补缩,产生缩孔缺陷。
3、冷硬层缺陷
冷硬层是指被注入到料筒内的Al液与料筒低温表面接触急速冷凝所形成的壳体(光谱仪检查冷硬层化学成分未发现异常,均在标准允许范围内),在高速填充时随Al液一起被填充到型腔。固态的冷硬层密度(2.7g/cm²)比液态(2.45g/cm²)的Al液大,在冲头低速运行阶段,冷硬层慢慢聚集在Al液的末端。冲头高速运行时,部分冷硬层将被卷入型腔,形成缺陷。最终残留在内浇口的冷硬层形态。冷硬层多为薄片状,表面有光泽且较硬,与周围母材多存在间隙,不仅影响外观,也降低铝合金压铸件的强度。
总结现有生产条件的不足及与夹渣的关联性,从而制定相应的改善措施,保证合适的模具温度,纠正错误的冲头润滑油供给方式,实现铝合金熔炼的标准化,并验证效果,使夹渣问题得到有效控制。

氧化夹渣的防止方法:
1.从冒口补浇金属液,改进冒口设计
2.炉料应清洁无腐蚀
3.铸件缩松处设置冒口,安放冷铁或冷铁与冒口联用
4.控制型砂水分,和砂芯干燥
5.采取细化品粒的措施
6.改进铸件在铸型中的位置降低浇注温度和浇注速度
氧化夹渣的消除夹渣的措施:
1、缩孔类夹渣的解决措施
缩孔类缺陷主要是压铸模具温度过高造成的,因此首先要确定压铸模具实际温度;其次,检查发现浇口附件的点式冷却水流量较小甚至堵塞,是铜管在使用过程中结垢 后截面减小所致。部分冷却水管长度比设计的短很多,这是因为压铸模具的冷却水铜管和冷却水孔都没有编号,在拆装压铸模具时会把长的铜管剪掉一部分后装到短 的水孔里,这样导致一些冷却水铜管较短,达不到冷却效果。
可采取两个措施:
- .在《模具保全检查项目表》中加入冷却水检查项目,规定冷却水流量检测方法及频率;
- .按照图纸要求检查冷却水铜管长度,不符合要求的予以更换,并对模具冷却水孔和冷却水铜管进行编号,一一对应。整改后,实测到的模具温度大幅度降低,几乎不再出现缩孔类夹渣。
2、油污类夹渣的解决措施
压铸润滑油采用花野275冲头润滑油,呈黑色粘稠状。脱模剂喷涂后,冲头退回进行料筒清扫,然后滴注冲头润滑油。现有的滴注位置为冲头前方的料筒底部,一般压铸润滑油用量为5mL/模。
3、氧化夹渣的3种解决措施:
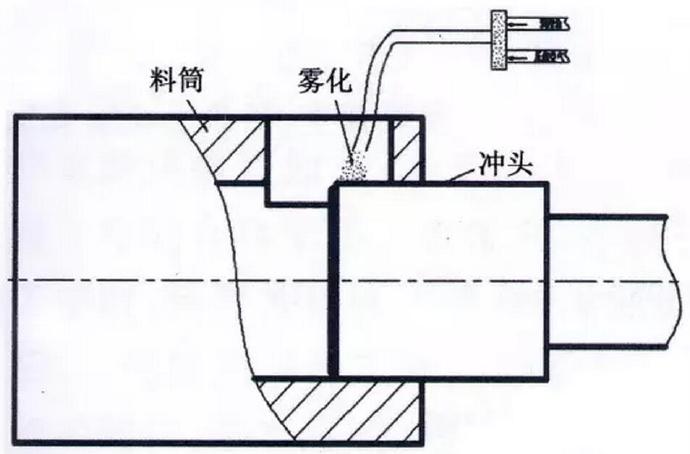
- 调整冲头润滑油用量冲头润滑油由5mL减少为4mL并无断料饼发生,当减少到3.5mL时偶尔会发生断料饼。分析发现冲头冷却水铜管大部分比设计值短,冷却效果不良。因此,恢复冲头冷却水管长度(距冲头内壁15mm),并纳入日常点检项目,再把润滑油用量降到3.5mL。
- 调整润滑油的加注位置及供给方式将原来的料筒底部加注润滑油改为冲头顶部加注。润滑油借助惯性顺流至整个冲头表面,润滑面积加大,便于燃烧。改善后的滴注位置见。
- 调整冲头润滑油供给方式虽然冲头顶部滴注润滑方式有较好的效果,但扩散不好,润滑面积不够,燃烧不完全。采用喷射可以在冲头表面形成雾化的油膜,扩散面积大,更利于燃烧,具有更好的润滑效果。经改善后,浇口断面比原来干净了很多,夹渣下降了将近90%,也没有出现断料饼现象。
4、硬层夹渣的解决措施:
调整压射延时
Al液注入到料筒后会在其接触面形成冷硬层,接触时间越长,产生的冷硬层就越多。因此,缩短压射延时,即缩短Al液与低温料筒接触时间是减少冷硬层的一个行之有效的方法。具体操作是将压射延时由原来的2.5s调整为0.5s。
调整汤勺退回待机时间
现场调查发现,由于操作者熟练程度参差不齐,导致铸造CT存在差异。若采用完全统一的工艺参数就会导致细节失误。如汤勺退回待机时间都设定为20s,对于不熟练工人来说,由于动作较慢,合模完毕时汤勺已经舀汤完成后在料筒上方等待了6s以上。根据操作者的熟练程度,灵活调整汤勺退回时间,汤勺在料筒上方等待时间控制在1s以内。并且,把汤勺退回待机时间纳入领工日常巡视项目,确保现场执行力。
过滤汤勺的应用
传统的汤勺在舀汤时不可避免的会舀入一些氧化层。采用过滤汤勺式样在舀Al液时可以有效避免氧化物被舀入,Al液的纯净度大大提高了。
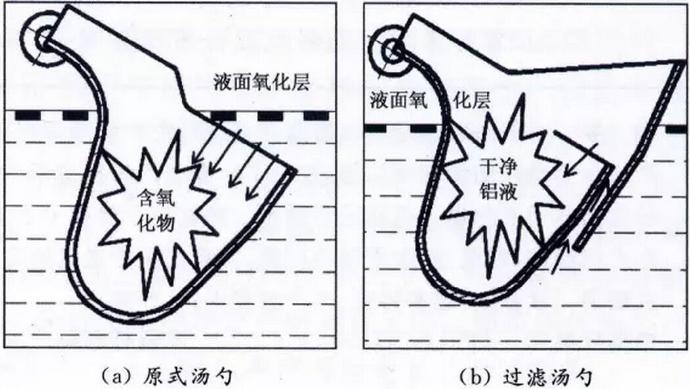
现有润滑油供给方式存在3个问题:
- .润滑油滴注在料筒底部很容易被浇注的Al液包裹而形成渣滓;
- .润滑油聚集在一块,短时间内无法完全燃烧,易被Al液包裹;
- .冲头顶部润滑效果不好,易导致不均匀磨损。此外,冲头油的用量也存在偏多的现象
规范Al液除渣除气作业要求
新旧炉料、除渣剂、除气剂和熔炼工具必须烘干;熔炼温度控制在750℃以下,避免Al液溶解过多的氢气;Al液转运之前应在转运包中进行旋转脱气和二次除渣处理,然后静置2h以上再对Al液应进行二次除气处理。这样提高Al液纯净度,减少Al液冷硬层。
氧化夹渣的防范措施:
1.炉料应经过吹砂,回炉料的使用量适当降低;
2.改进浇注系统设计,提高其挡渣能力。
3.采用适当的熔剂去渣。
4.浇注时应当平稳并应注意挡渣。
5.精炼后浇注前合金液应静置时间。
6.控制回炉比例。
7.对合金液精炼除渣、除气。
8.清理模具型腔,降低保温温度和减少保温时间。
9.熔炉要定期全面清理,清除底部沉积的“淤泥”,也就是比重较重的氧化物杂质
10.还有料温的控制,熔炼及浇注料温太低,容易析出初晶硅,形成硬质点
11.采取倾斜浇注系统,使液流平稳,不产生二次氧化
12.设计的浇注系统必须有稳流、缓冲、撇渣能力。